Solid-state batteries (SSBs) are emerging as the next-generation energy storage solution, offering significant improvements over traditional lithium-ion batteries. With the promise of higher energy density, enhanced safety, and longer lifespan, solid-state batteries are attracting increasing attention from a wide range of industries, from electric vehicles (EVs) to aerospace and medical devices. In this paper, we explore the fundamentals of solid-state batteries, the current market status, technological challenges, prospects, and their impact on various industries.
What is Solid State Battery?
Lithium-ion batteries are widely used as power sources for transportation due to their long lifespan and high energy density. However, in recent years, safety incidents related to lithium-ion batteries have occurred frequently.
The primary reason behind these incidents is that traditional liquid lithium-ion batteries use organic solvents as electrolytes. Most common electrolytes contain highly flammable substances, which can lead to fire hazards, spontaneous combustion, and even explosions. To address these safety concerns, researchers and industry professionals have turned their attention to solid-state batteries, which replace liquid electrolytes with non-flammable solid electrolytes, significantly improving battery safety.
Lithium-ion batteries can be categorized into two main types based on their electrolytes: liquid lithium batteries and solid-state batteries. Solid-state batteries include semi-solid-state, quasi-solid-state, and all-solid-state batteries. Semi-solid-state batteries act as a transitional stage between liquid and fully solid-state batteries. The commercialization of semi-solid-state batteries provides a buffer period, allowing for the early development of an all-solid-state battery supply chain. As technology advances, hybrid solid-liquid batteries will gradually reduce liquid electrolyte content, ultimately achieving fully solid-state battery technology.
Lithium-Ion Battery Categories
While global standards exist, different codes and policies are prioritized by different regions, often causing delays in international battery trade.
1. Liquid Lithium Batteries
Contains only liquid electrolytes with no solid electrolytes. Includes both liquid lithium-ion batteries and liquid metal lithium batteries.
2. Gel Electrolyte Lithium Batteries
A subtype of liquid lithium-ion batteries where the electrolyte is in gel form. Contains no solid electrolyte.
3. Semi-Solid-State Batteries
Contains both solid and liquid electrolytes, with a higher proportion of liquid electrolytes. Typically, liquid electrolyte makes up 5%–10% of the total battery composition.
4. Quasi-Solid-State Batteries
Feature a higher proportion of solid electrolyte while still containing a small amount of liquid electrolyte. Liquid electrolyte content is typically between 0%–5%.
5. Hybrid Solid-Liquid Lithium Batteries
Contains a mix of both liquid and solid electrolytes. Semi-solid-state and quasi-solid-state batteries fall into this category.
6. All-Solid-State Batteries
Constructed entirely with solid-state electrodes and solid electrolytes. Contain no liquid electrolyte at any temperature. Sometimes referred to as “all-solid-state electrolyte lithium batteries.” If rechargeable, they can be further classified as “all-solid-state lithium secondary batteries”.
Solid-state batteries have a simpler structure compared to traditional liquid-based batteries. The solid electrolyte not only conducts lithium ions but also serves as a separator. In fully solid-state batteries, there is no need for liquid electrolytes, electrolyte salts, separators, or adhesive materials like polyvinylidene fluoride (PVDF), significantly simplifying the battery construction process.
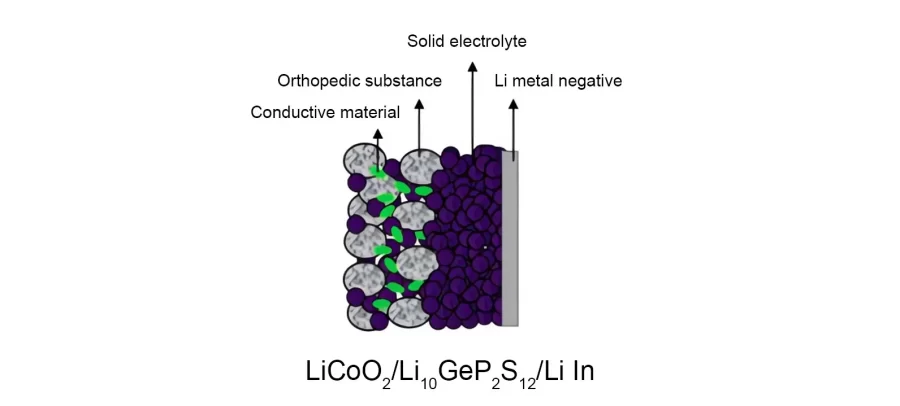
How does Solid State Battery Work?
The working principle of solid-state batteries is similar to that of liquid-based batteries. During charging, lithium ions are extracted from the crystal lattice of the active material in the cathode and migrate to the anode through the solid electrolyte, while electrons travel to the anode via an external circuit. At the anode, the lithium ions and electrons recombine to form lithium atoms, alloy with the anode material, or become embedded within it. The discharge process is the exact opposite of charging, with electrons flowing through the external circuit to power electronic devices.
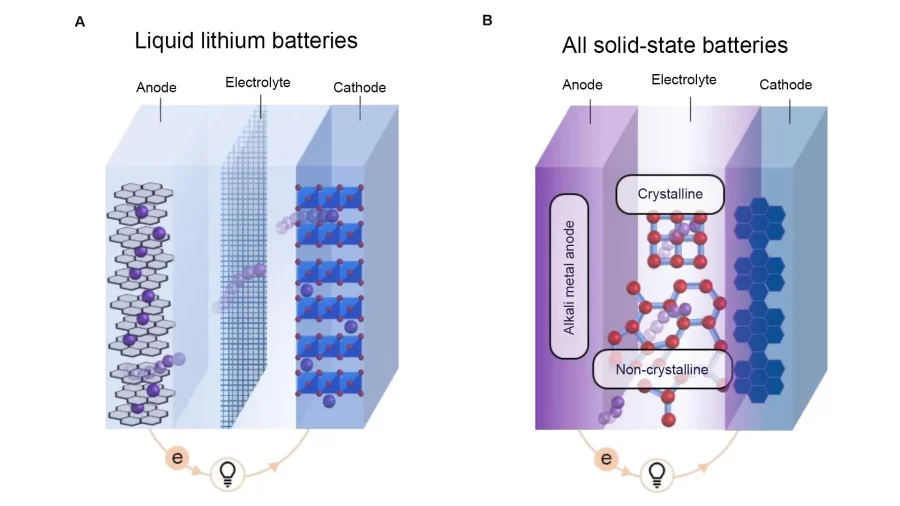
Comparison of the Properties of Liquid Lithium Batteries, Semi-Solid State Batteries, and Solid State Batteries.
Property | Liquid Lithium-ion Battery | Semi-Solid-State Battery | All-Solid-State Battery |
Electrolyte Type | Liquid Electrolyte | Liquid Electrolyte + Solid Electrolyte | Solid Electrolyte (including Polymer Solid Electrolytes, Oxide Solid Electrolytes, Sulfide Solid Electrolytes, etc.) |
Anode Material | Graphite Anode or Silicon Carbon Anode | Graphite Anode or Silicon Carbon Anode | Graphite Anode, Silicon Carbon Anode, or Metallic Lithium |
Separator | Has a Separator | Has a Separator, Coated with Solid Electrolyte Material | No Separator |
Safety Performance | Relatively Poor Safety | Improved Safety | High Safety |
Energy Density | Up to 300 Wh/kg | Up to 400 Wh/kg | Up to 500 Wh/kg or More |
What are the Advantages of Solid State Batteries?
Solid-State Batteries Offer More Safety
Traditional lithium-ion batteries, which use flammable organic electrolytes, can pose risks such as overheating, self-ignition, or even explosion in cases of overcharging or internal short-circuiting. In contrast, most solid-state electrolytes are high-temperature resistant and non-flammable, significantly reducing the risk of battery fires or explosions. However, it’s important to note that no battery can be considered safe from a thermodynamic perspective. The actual safety of a battery is influenced by various factors, including the electrolyte and electrode materials, quality control during manufacturing, and the battery management system (BMS). While solid-state electrolytes greatly enhance safety at the fundamental level, quality control during production and the effectiveness of the BMS remain crucial.
Solid-State Batteries With Higher Energy Density
Semi-solid-state batteries offer higher energy density compared to traditional liquid batteries. Companies like Weilan New Energy and Guoxuan High-Tech have developed semi-solid-state batteries with an energy density of 360 Wh/kg. Solid-state electrolytes typically have a wider electrochemical window, allowing compatibility with more high-voltage cathode materials (such as high-nickel cathodes and nickel-manganese spinel cathodes). Additionally, the higher voltage and better safety of solid-state batteries enable a simpler battery management system (BMS), further improving the energy density of the battery system used in electric vehicles (EVs).
Solid-State Batteries Offer Ultra-Fast Charging Times
According to recent studies, Solid-state batteries can charge up to six times faster than current commercial battery technologies. However, this number varies, depending on how developers advance and optimize the new technology. Prototype solid-state batteries with very high charging speeds already exist. Yet they often significantly compromise other important performance parameters, such as energy density, life span, and safety. To determine the best alternative, we must balance this advantage against other essential characteristics these batteries need to possess, including cost considerations.
So far, liquid electrolytes degrade at high temperatures, while solid electrolytes perform better under heat. This inherent advantage suggests that solid-state batteries may sustain higher performance during fast-charging cycles, where heat generation is typically higher.
Additionally, the researchers are working to enhance the ionic conductivity of solid electrolytes to further optimize charging speeds without sacrificing safety or durability.
Solid-State Batteries Allow for More Flexible Grouping Designs
Manufacturers can group solid-state batteries in an internal series configuration. By connecting the battery’s electrodes in series inside the cell, this design increases the voltage of a single battery, matching the voltage level of multiple series-connected cells. This internal series design reduces the need for additional packaging and increases the efficiency of the grouping process.
Solid-State Batteries Could Advance Electric Vehicle Battery Technology
Beyond safety and energy density, EV battery systems require many other features, such as long cycle life, wide operating temperature ranges, resistance to compression, and vibration. Solid-state batteries could address these demands in the following ways:
- High Energy Density: High-energy-density compounds and sulfur-based materials could be used as cathodes.
- High Volume Energy Density: Dense thin-layer electrolytes and high-density cathodes could be employed.
- Long Cycle Life: By controlling the volume expansion of the anode and cathode, and maintaining stable interface contact, technologies like composite electrodes and flexible or gel-like interfaces can enhance cycle life.
- Wide Temperature Range: Superionic conductors, solid-liquid hybrids, and advanced thermal management techniques could help the battery function in temperatures ranging from -70°C to 150°C.
- Improved Compression Resistance: Non-powdering lithium-metal composite electrodes and non-oxidizing, non-flammable solid-state electrolytes could improve puncture resistance.
- Better Vibration Resistance: Incorporating flexible materials or shock-absorbing systems could improve vibration tolerance.
- Cost Reduction and Mass Production: By enhancing energy density and cycle life, solid-state batteries can make use of readily available raw materials, simplifying manufacturing. The electrode and electrolyte layers are easier to process, allowing faster production of the cells.
Basic requirements for battery applications and possible solution ideas for solid-state batteries
Performance Requirement | Possible Solid-State Battery Solutions |
High Gravimetric Energy Density | Use high-energy-density embedded compounds, sulfur-based materials, or air-based cathodes. |
High Volumetric Energy Density | Utilize dense thin-layer electrolyte technology and high-compaction embedded compound cathodes. |
Long Cycle Life | Control volume expansion of electrodes and maintain stable interface contact using composite electrodes, flexible materials, amorphous structures, or gel-like interfaces. |
Minimal Volume Change | Implement buffering mechanisms to accommodate volume changes, such as composite electrodes. |
Wide Operating Temperature (-70 to 150°C) | Use superionic conductors, solid-liquid hybrid electrolytes, and advanced thermal management solutions. |
High Power Capability | Design high-rate-capable electrodes, incorporate polymer or disordered-layer structures, optimize solid-liquid interfaces, and use high-ion-conductivity composite materials with thin-film technology. |
Resistance to Compression & Puncture | Use lithium-metal composite electrodes that resist pulverization and solid electrolytes that are non-oxidizing, non-flammable, and non-explosive. |
Vibration Resistance | Integrate flexible materials or built-in shock absorption systems. |
Overcharge Protection | Use electrolytes with a wide electrochemical stability window along with compatible cathode materials. |
Over-discharge Protection | Select highly stable anode and cathode materials. |
Short-circuit Resistance | Implement built-in fuse and thermal protection mechanisms within the battery cell. |
No Internal Short Circuits | Develop mechanisms to suppress lithium dendrite growth and prevent puncturing. |
High Energy Efficiency | Minimize interfacial resistance in electrodes, electrolytes, and interfaces; reduce electrochemical and diffusion polarization in the cathode. |
Low Self-Discharge Rate | Prevent lithium dendrite formation and avoid continuous interfacial reactions. |
Low Cost & Mass Production Feasibility | Enhance energy density and cycle life to reduce costs; use readily available raw materials; ensure that electrode sheets and electrolyte layers/membranes are easy to process; streamline cell manufacturing for rapid production. |
Cost: The cost of semi-solid-state battery cells is projected to be 0.5729 RMB/Wh during large-scale production, which is slightly lower than the 0.5766 RMB/Wh cost for liquid battery cells. While semi-solid-state battery components are made from conventional materials, making them less expensive than liquid batteries, the higher environmental control requirements during manufacturing do slightly increase production costs.
Cost Comparison: Semi-Solid vs. Liquid Batteries
Battery Type | Cell BOM Cost (CNY/Wh) | Separator/Solid Electrolyte Film Cost Ratio | Electrolyte/Solidifier Cost Ratio | Total (Film + Electrolyte) Cost Ratio | Total (Film + Electrolyte) Cost (CNY/Wh) |
Traditional Liquid Battery (Ternary + Carbon) | 0.5766 | 7.65% | 12.20% | 19.85% | 0.1145 |
Semi-Solid Battery (Ternary + Carbon) | 0.5729 | 12.32% | 7.02% | 19.34% | 0.1108 |
Are There Any Commercial Solid-State Batteries?
While solid-state batteries are still in the developmental phase, several companies have made significant strides toward commercialization. Currently, most solid-state battery applications are limited to prototypes and small-scale production rather than mass-market products. However, industry leaders and startups alike are making promising advancements.
The 2025 “China All-Solid-State Battery Industry-Academia-Research Collaborative Innovation Platform” Annual Conference and the 2nd China All-Solid-State Battery Innovation Development Summit Forum were held in Beijing from February 15 to 16. The forum brought together numerous industry experts and corporate representatives to discuss the latest advancements and prospects of all-solid-state battery technology.
Wang Deping, Chief Scientist of China First Automobile Works (FAW) and Director of the National Key Laboratory of High-End Vehicle Integration and Control at FAW R&D Institute (Science & Technology Innovation Management Division), delivered a keynote speech. He revealed that FAW has been dedicated to all-solid-state battery research since 2014, focusing on vehicle requirements. FAW plans to begin small-scale applications of all-solid-state batteries in 2027.
Academician Ouyang Minggao’s Industry Outlook
The Academician Ouyang Minggao Research Station predicts that mass production of all-solid-state batteries will begin in 2030, with pilot production launching as early as 2027. The total industry output is expected to exceed 100 billion yuan (approx. $14 billion) by 2030.
BYD’s All-Solid-State Battery Plan
BYD aims to begin the small-scale production of sulfide-based all-solid-state batteries by 2027 and plans to integrate them into mainstream electric vehicles by 2030.
CATL’s Solid-State Battery Progress
Wu Kai, Chief Scientist at CATL (Contemporary Amperex Technology Co. Ltd.), previously stated that the company’s all-solid-state battery technology is currently at a 4 out of 10 level. CATL’s goal is to reach a 7–8 level by 2027, which would enable small-scale production.
EVE Energy’s Two-Phase Strategy
EVE Energy has outlined a two-step strategy for all-solid-state battery development:
2026: Achieve process breakthroughs
2028: Attain full technological breakthroughs and launch high-energy-density 400Wh/kg all-solid-state batteries
Going High-Tech & Changan Auto’s Solid-State Battery Plans
Going High-Tech: Plans to begin small-scale vehicle testing of solid-state batteries in 2027 and achieve mass production by 2030.
Changan Auto: Aim to introduce eight self-developed battery cells by 2030, covering liquid, semi-solid, and solid-state batteries.
With leading automakers and battery manufacturers accelerating their solid-state battery R&D efforts, 2027 is shaping up to be a pivotal year for small-scale production, with 2030 marking the beginning of large-scale commercialization. These developments will enhance EV performance, safety, and energy density, paving the way for the next generation of battery technology.
Four Key Challenges of Solid-State Batteries
Technical Challenges
Optimization of Solid Electrolyte Performance
- Insufficient Ionic Conductivity:
The ionic conductivity of current solid electrolytes is generally lower than that of liquid electrolytes, especially at room temperature. This results in slower charging and discharging rates, affecting the battery’s power performance and making it difficult to meet the demands of high-power applications, such as fast charging and rapid acceleration in electric vehicles. For instance, oxide-based solid electrolytes typically have lower conductivity, limiting their application in high-performance batteries.
- Stability Issues:
Some solid electrolytes may undergo structural changes or decomposition during battery operation, affecting long-term stability and cycle life. For example, sulfide-based solid electrolytes are highly sensitive to air and can react with moisture and oxygen, producing toxic hydrogen sulfide gas. This not only complicates manufacturing and storage but also raises safety concerns.
- Interface Challenges:
One of the biggest challenges in solid-state batteries is the poor interface contact between electrodes and solid electrolytes. Due to the rigid nature of solid electrolytes, the contact area between the electrode and electrolyte is relatively small, resulting in high interfacial resistance. This reduces charging/discharging efficiency and leads to interface stress during cycling, which can cause delamination and detachment, ultimately degrading battery performance and lifespan.
Compatibility of Electrode Materials
- Compatibility of Electrode Materials
In solid-state batteries, cathode materials must be highly compatible with solid electrolytes while also offering high specific capacity and good rate performance. However, commonly used cathode materials may undergo chemical reactions or structural degradation when paired with solid electrolytes, negatively impacting battery performance.
- Anode Materials:
Silicon-based anodes have an exceptionally high theoretical capacity, making them an ideal choice for solid-state batteries. However, silicon undergoes massive volume expansion (up to 300%) during charging and discharging, which can lead to electrode cracking and structural failure, reducing the battery’s cycle life.
Lithium metal anodes offer even higher energy density, but they face the formation of lithium dendrites, which can pierce the solid electrolyte, causing short circuits and serious safety risks.
Manufacturing Process Challenges
Fabrication of Solid Electrolyte Membranes: Producing high-quality, uniform, and precisely controlled-thickness solid electrolyte membranes is a crucial step in solid-state battery manufacturing. Current fabrication methods—such as sol-gel processing, magnetron sputtering, and cold pressing—face challenges like complex procedures, high costs, and low production efficiency, making it difficult to scale up for mass production.
Battery Assembly Process: Solid-state battery assembly must be conducted in an oxygen-free, dry environment, which places extremely high demands on production equipment and processes. Traditional lithium-ion battery assembly equipment and techniques cannot be directly applied to solid-state battery manufacturing, requiring significant modifications and process optimizations, which in turn increase production costs and complexity.
Continuous Densification Technology: Achieving continuous densification of the electrode and solid electrolyte layers is essential for improving both battery performance and production efficiency. However, current technologies still face challenges in ensuring uniform and defect-free densification, which remains a bottleneck affecting the yield and efficiency of solid-state battery manufacturing lines.
Cost Challenges
High Raw Material Costs: The materials used in solid-state batteries—such as solid electrolytes and high-performance electrode materials—have higher production costs compared to traditional lithium-ion batteries. For example:
- Sulfide-based solid electrolytes require expensive raw materials and complex synthesis processes, keeping their costs relatively high.
- Lithium metal anodes have significant production costs, and the limited supply of lithium resources may further restrict large-scale adoption.
High Equipment and Production Costs: Since solid-state battery manufacturing processes differ significantly from traditional lithium-ion batteries, new production equipment and specialized manufacturing lines must be developed. This leads to a substantial increase in capital investment. Additionally, to maintain the required dry and oxygen-free production environment, manufacturers must also install specialized auxiliary equipment and facilities, further driving up overall production costs.
Industry Chain Coordination Challenges
Underdeveloped Industry Chain: The solid-state battery industry is still in its early stages, and there is a lack of effective collaboration among upstream and downstream enterprises. For example:
- Insufficient communication and cooperation between solid electrolyte material suppliers and battery manufacturers result in materials that fail to meet production quality and performance requirements.
- Weak technical integration between manufacturing equipment suppliers and battery producers hinders the development and optimization of production equipment, slowing down industrial progress.
Lack of Standards and Regulations: Currently, solid-state battery technology lacks well-established industry standards and regulations, making it difficult to evaluate product quality, conduct performance testing, and ensure safety certification. This gap also impedes large-scale commercialization and widespread market adoption of solid-state batteries.
Solid-state batteries hold immense promise for the future of energy storage, with superior safety, performance, and efficiency over traditional lithium-ion batteries. While challenges remain, continuous advancements in materials, manufacturing, and cost reduction are bringing this revolutionary technology closer to commercial reality. With major industry players investing heavily in R&D, solid-state batteries are set to transform the landscape of electric vehicles, medical devices, and high-performance electronics within the next decade.
CM Batteries specializes in custom battery pack solutions for industries requiring high-performance, tailored energy storage. As solid-state battery technology evolves, CM Batteries remains committed to delivering cutting-edge, application-specific energy solutions for the future. If you need to know more, you can contact our professional consultants today!