At the heart of the battery industry lies an essential lithium-ion battery assembly process called battery pack production. In this article, we will explore the world of battery packs, including how engineers evaluate and design custom solutions, the step-by-step manufacturing process, critical quality control and safety measures, and the intricacies of shipping these batteries.
How do Engineers Evaluate Lithium-Ion Battery Pack Design?
The type of battery development and the technologies involved vary depending on the specific application. The battery design engineer will judge the design based on two common scenarios:
- Basic Lithium Battery Pack Design: These custom battery packs are made to fit into existing hard enclosures that protect the battery. In this case, the customer would request a specific battery size, and the supplier would build that battery. Once the customer confirms the details, Once the customer confirms the details, it usually takes 7-10 working days to follow the li-ion battery pack design and develop a custom.
- Advanced Lithium Battery Pack Design: These custom batteries are made when the customer has special requests for temperature capabilities, dimensions, discharge current, and/or battery cycles. In this case, our chemistries, enclosure, and battery management system (BMS) experts are required to monitor each project closely. These batteries can take longer to produce, and a custom timeline is typically created that suits the specific requirements for this type of battery development and prototype creation.
Evaluate Battery Chemistries:
Battery chemistries refer to the composition of the materials in each battery, commonly including alkaline, nickel-metal hydride (NiMH), and lithium-ion. Different battery chemistries offer varying advantages, and performance characteristics are often decided based on factors such as the working voltage platform, dimensions, working time, and cost-performance ratio. CMB’s battery pack designer gives priority to the following three most common battery cells for the battery pack design: INR (Ternary Lithium), LFP (Lithium Iron Phosphate Chemistry) and LiPo(Lithium Polymer).
Evaluate Battery Casing Design:
Designing an enclosure for the custom lithium-ion battery packs considers several factors, including the work environment and function of the battery. The purpose of the enclosure is to protect the battery from external conditions like weather and internal issues like battery malfunctions. The enclosure holds the entire battery, including electronic circuits, interconnections, and connectors, so it must be built to accommodate these features:
- The corrosiveness of the sea
- Thermal expansion in colder environments
- Durability in load-bearing environments
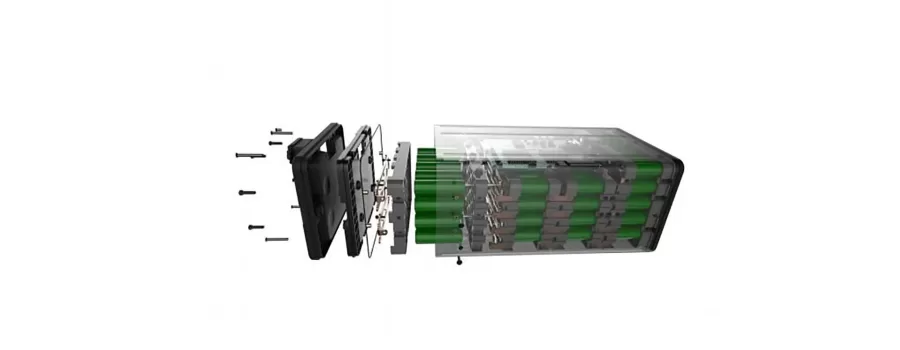
Currently, most enclosures for custom batteries are made of ABS plastic that is durable to impact and resistant to alkaline solutions. If you’re looking for higher quality and durability, you can also opt for alternative materials.
Evaluate Battery Management System:
BMS is the heart of a custom battery. A professional pack engineer can provide the best BMS design for your battery.
- A standard 1-7S BMS is the most common in the market. At CMB, you do not need to pay any extra BMS development fees for 1-7S BMS.
- A 7-16S BMS, or Smart BMS, is equipped with CANBUS, UART 485, and RS232 communication to ensure long-term battery health and optimal function. Smart BMS can require additional development fees. However, at CMB, we offer discounted or waived development fees for certain order sizes.
The CMB Lithium Ion Battery Manufacturing Process
A battery pack consists of multiple cells connected in series or parallel. How to make lithium-ion batteries? It’s always been an interesting topic. The production of lithium-ion batteries is a complex process, totaling Three steps.
Step One: Cell Sorting
The cell sorting stage is a critical step in ensuring the consistent performance of lithium-ion batteries. The lithium-ion battery manufacturer should have a strict gap standard of less 5mv voltage gap, less 15mΩ internal resistance, and less 5mAh capacity gap.
To ensure the li-ion battery with a long-lasting cycle and reliable performance, the cell sorting process should be very strict. But before this lithium-ion battery manufacturing process, the custom li-ion battery factory should have the advantage of li-ion cell supply chain. We only do business with the brand cell factory or big wholesalers directly to ensure the sources of the cells are from the original cells factory. As one battery pack manufacturer, who can ask the original 18650 cell or 21700 cells factory as our cell gap standards to meet custom battery pack solutions’ request?
Step Two: Lithium Battery Pack Assembly
The battery pack assembly is the process of assembling the positive electrode, negative electrode, and diaphragm into a complete battery. This involves placing the electrodes in a cell casing, adding the electrolyte, and sealing the cell.
Lithium-ion batteries are usually produced using two lithium-ion battery assembly process methods: manual assembly and automated assembly.
Manual assembly is the most common technology for battery assembly, it is relatively low-cost and flexible and can be adapted to different types of batteries. The only bad point is that since it is a manual assembly, the precision finish may not be high, which also reflects the importance of ISO9001 production standard management in assembling lithium-ion battery factories. The other kind of automated assembly is an emerging technology in battery assembly. As it is machine-operated, it can reduce human error and improve production efficiency while improving the accuracy of completion, but the cost is relatively high and the flexibility is poor, which is not suitable for small batch production.
Battery assembly requires attention to the following points:
- The thickness and area of the positive and negative electrodes must be uniform.
- The thickness and aperture of the diaphragm must meet the requirements.
- The concentration and type of electrolyte must be correct.
- The sealing of the battery must be firm and reliable.
- Introduce tools concept to improve the battery pack assembly reliability.
The quality of battery assembly has a significant impact on the performance and safety of the battery. If the battery is not properly assembled, it will lead to a decrease in capacity, lower discharge rate, shorter cycle life, reduced safety, and other problems.
Step Three: Battery Pack Insulation
Battery pack insulation is very important. When the battery pack poles have a higher discharge current it causes the temperature high. We should make the battery pack insulation to avoid the li-ion battery pack fire or short circuit.
The main role of the battery pack insulation process includes:
- Improve the performance of the battery: The battery pack insulation process can improve the conductivity, corrosion resistance, heat resistance, and oxidation resistance of the battery, thus improving the capacity, discharge rate, cycle life, and safety of the battery.
- Prevents short circuits: Short circuits can cause fires and explosions, so it is important to prevent them from happening. Battery pack insulation can help to prevent short circuits by keeping the battery cells electrically isolated from each other.
- Extends battery life: The battery pack insulation process can protect the battery from the damage of external factors, such as water, dust, acid, and alkali, to extend the service life of the battery.
- Beautify the battery: The battery pack insulation process can make the appearance of the battery more beautiful and increase the added value of the battery.
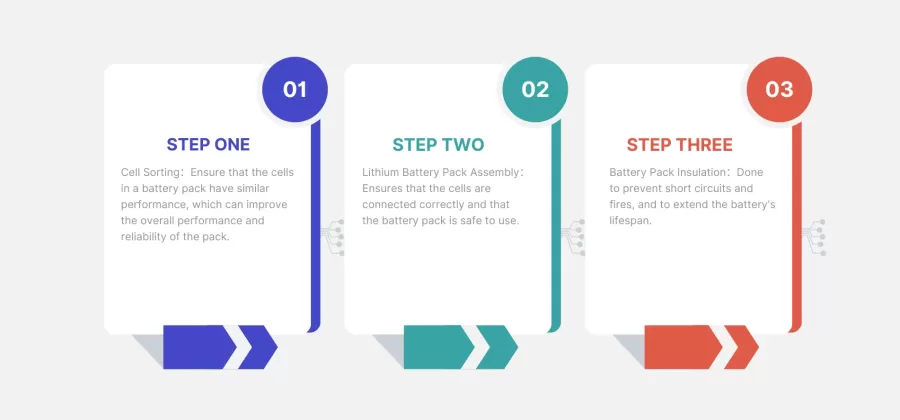
Battery Manufacturing Quality Control
Strict quality control protocols are crucial throughout the entire lithium-ion battery manufacturing process. From the procurement of battery cells, battery PCBs, BMS, and other accessories to assembly and testing, we are meticulous in every step.
To achieve this, manufacturers implement critical quality checkpoints, tests, and inspections at each stage of production.
Stage | Check List | Machines |
Raw materials | The original brand cells factory and cell specification | Battery Internal Resistance Tester/Aging Machine |
Cell Sorting | BOM standard Guidance Manual | Cell Sorting Machine |
Battery assembly | Welding and Insulation Process | Welding machine and aging machine |
Battery testing | Capacity, Discharge rate, Cycle life, Safety | Aging machine and comprehensive test machine |
These are just some of the most common checkpoints, tests, and inspections that are performed during lithium-ion battery pack production. The specific tests and machines that are used will vary depending on the specific battery design and application.
It is important to note that quality control is essential throughout the entire lithium-ion battery production process. By implementing strict quality control measures, manufacturers can help to ensure that their batteries are safe and reliable.
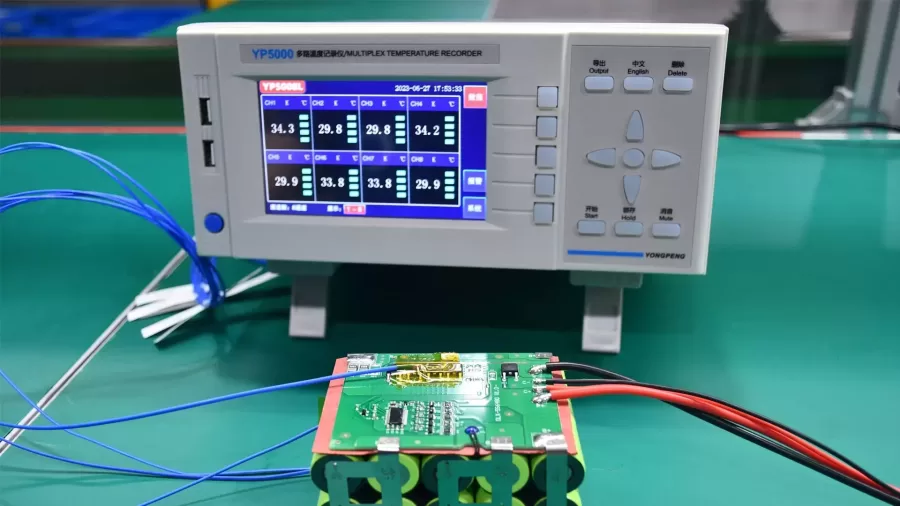
Shipping Lithium-Ion Batteries Production
The final step in the process of delivering a customized battery pack to a customer is shipping. At CMB, we offer a wide range of international shipping options to meet each customer’s unique needs. Our shipping process includes:
Dangerous Goods Certification: If a customer requires a Dangerous Goods Certificate, we apply for one on their behalf at no additional charge. This ensures compliance with international shipping regulations for lithium-ion batteries.
Careful Packing: Our batteries are packed carefully into pallets to ensure safe and secure transportation. Our packages are verified by customs authorities, ensuring they meet international standards. This minimizes the risk of damage during transit.
Tracking and Updates: Once the order is shipped, we provide tracking information to our customers. We keep them regularly informed of the progress of their shipment, ensuring transparency throughout the delivery process.
Customer Support: Our team remains available to address any questions or concerns about the shipping process, providing peace of mind to our customers.
By offering comprehensive shipping services, we ensure that our high-quality, custom battery packs reach our customers safely and efficiently, completing the production and delivery process.
In conclusion, Battery pack production is a complex and multifaceted process that requires meticulous attention to detail, strict quality control, and a commitment to safety. By complying with strict quality control standards and advances in lithium battery technology, battery pack manufacturers can produce high-quality, safe, and reliable battery packs that power our modern world. Let me know if you have any other questions.
2 thoughts