Testing is an essential step in manufacturing safe, efficient, and long-lasting lithium-ion batteries. Here’s what manufacturers should be testing on every battery pack they produce.
Manufacturing lithium-ion (Li-ion) batteries is a profession that comes with a great deal of responsibility. Batteries that are not produced with certain factors and standards in mind can result in faulty performance, shortened battery lifespans, and even hazardous situations. To ensure the safety of consumers, there are a number of certifications that different markets require when it comes to Li-ion batteries, including UN38.3, IEC62133, UL, and CE. These certifications put into place battery pack testing standards for lithium-ion battery pack manufacturers to adhere to. Here’s what your battery manufacturer should be assessing during the battery testing process.
What’s Assessed During Lithium-Ion Battery Pack Testing?
1. Raw Materials (Cell, BMS, and Charger)
Raw material testing involves the pre-production assessment of a battery pack’s cells, battery management system (BMS), and charger. During this process, cells should be inspected with an internal resistance tester, BMS’s should be evaluated via a protection board tester, and chargers should be assessed with a power meter to check the charger’s specifications. In accordance with lithium-ion battery testing standards, raw material testing is a very important step in the pre-production of battery packs.
2. The Sorting Process & Automatic Sorting Machines
Battery sorting is the first step in the battery pack manufacturing process. In this phase, batter cells are sorted by voltage, capacity, and internal resistance and then grouped for assembly into packs. Whether done by hand or by automated machine, testing and auditing this process is essential to ensure consistency, safety, and reliability in manufactured battery packs.
3. The Spot Welding Process & Spot Welding Machines
In battery manufacturing, spot welding is the process of joining battery cells together via a connective nickel strip. This can be done by hand, by machine, or by a combination of both. There are four types of spot welding machines: automatic, semi-automatic, full-automatic, and pneumatic. Spot welding is a serious and integral process in battery pack manufacturing. Spot welding machines should be maintained every week and the spot welding needle should be changed according to each nickel strip’s specifications. Evaluating this process and any machinery involved in it ensures accurate assembly of lithium-ion battery packs.
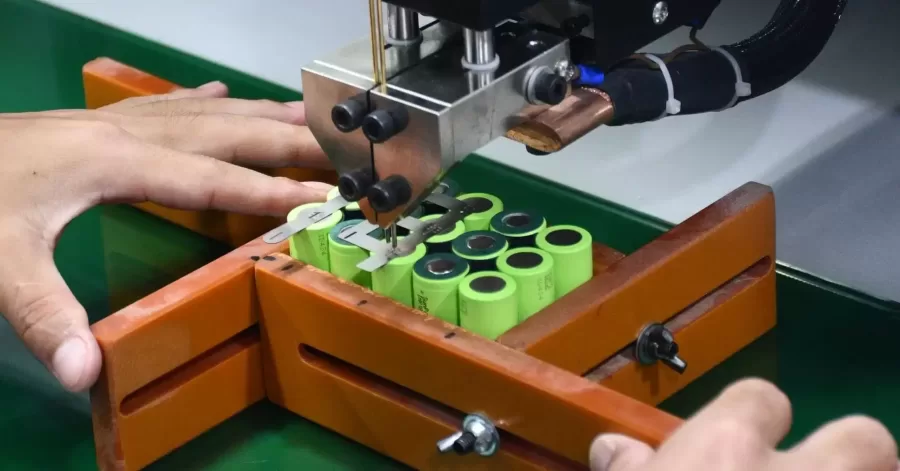
4. Charge-Discharge & Aging
A charge-discharge aging test evaluates how many cycles a battery pack can endure by repeatedly charging and discharging it until its performance declines. During charge-discharge aging tests, a battery pack’s voltage, capacity, maximum continuous discharge, maximum continuous charge, battery cycles, spot welding, and BMS assembly are all evaluated.
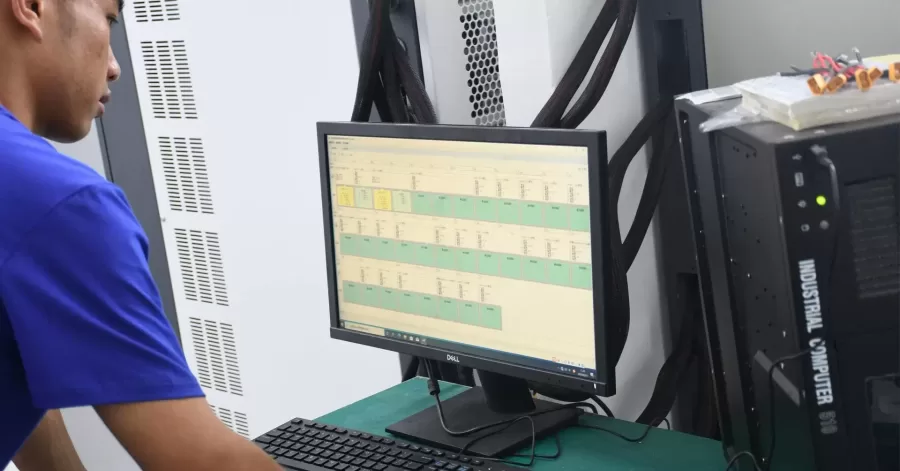
5. Temperature and Humidity Tolerance
Temperature and humidity fluctuations can directly affect the chemistry of Li-ion batteries, leading to changes in performance and shortened life cycles. A constant temperature and humidity tester is a machine that simulates different environmental conditions, testing battery performance at different temperature and humidity levels. This process is helpful in analyzing and modifying battery pack designs to ensure the best performance and reliability.
6. Vibration Tolerance
During vibration testing, technicians simulate real-world operating conditions to evaluate lithium-ion battery performance. They inspect spot welds, connector interfaces, and wiring to ensure structural integrity and reliability. This testing ensures the structural integrity and durability of a battery pack.
7. Electronic Load
An electronic load test simulates the real-time working environment of a battery pack while assessing its electronic performance and protective features, such as overvoltage protection, overcurrent protection, over power protection, voltage reversal, and over temperature protection.
8. Voltage Levels
During the testing process, it’s standard to assess the levels of voltage in a battery pack’s cells. If technicians detect a voltage gap in a battery pack, they use a DC power supply to charge the lower-voltage cells until their levels match those of the higher-voltage cells. This process effectively restores balance and resolves the issue.
9. Battery Load
Battery load testing evaluates the output data of a battery pack to determine its performance under operational conditions. This process involves the use of battery load meters, which assess the pack’s ability to deliver power consistently. These tests help ensure the safety, reliability, and overall quality of the battery pack.
10. Comprehensive Battery Testing
Before shipment, all battery packs should be assessed with a comprehensive battery tester. These devices evaluate internal resistance, discharge protection, short circuit protection, cut-off delay protection, and more.
11. Diagnostics
When a battery pack fails to perform properly during evaluation, technicians often use a multimeter to identify the root cause. They measure the voltage, resistance, and current of individual cells to pinpoint the source of the problem—whether it lies in the cells themselves or in the battery management system (BMS). These test results help guide accurate and effective repairs.
Designing and manufacturing lithium ion batteries requires specialized expertise and an unwavering commitment to quality. Every battery pack manufacturing step, including thorough testing with advanced lithium-ion test equipment, is important to guarantee consistent quality and dependability.
At CMB, our lithium ion battery testing is integrated into our production process, and our engineering team conducts these extensive tests in our on-site laboratory. When seeking a reliable lithium-ion battery manufacturer, be sure to select a partner that is thorough with their testing process to ensure your end products are reliable, efficient, long-lasting, and safe. If you’d like to learn more about CMB’s battery testing process or are interested in our customizable battery manufacturing services, reach out to a CMB representative today.
2 thoughts