Choosing the Right Connection Method for Battery Components: Ensuring Lithium Battery Pack Reliability with Spot Welding vs Soldering. This article delves into the principles, processes, advantages, and limitations of both methods, with a particular focus on spot welding and its role in custom battery pack manufacturing.
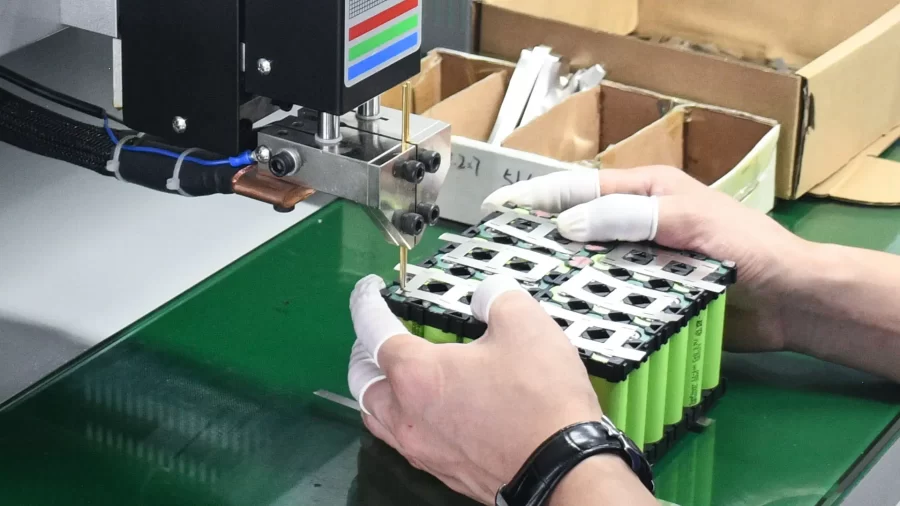
Principles of Spot Welding in Lithium Battery Production
Spot welding for batteries is a resistance welding technique that uses electrical current to generate heat at the point of contact between two metal surfaces. The process involves passing a high current through electrodes that clamp the materials together, causing localized melting and fusion.
The basic formula for heat generation in resistance welding is:
Q = I^2Rt
Where:
Q = Heat generated (J)
I = Welding current (A)
R = Resistance between electrodes (Ω)
t = Welding time (s)
This equation highlights the three main factors influencing spot weld lithium batteries: current, resistance, and time.
Spot Welding Process
Spot welding typically consists of five stages:
Pre-pressure stage
- Material Preparation: Select the appropriate metal sheets or components and ensure the surfaces are clean and free of grease, oxides, or other contaminants.
- Electrode Preparation: Choose the right electrode material and shape, make sure the electrode surface is smooth, and adjust the electrode pressure as needed.
Clamping Stage
- Positioning and Clamping: Place the materials to be welded between the electrodes of the spot welding machine. Adjust the position to ensure the welding point is directly under the electrode.
- Applying Pressure: Use a mechanical or pneumatic system to apply pressure, ensuring the electrodes make firm contact with the materials.
Current Application Stage
- Setting Parameters: Set the welding current, time, and electrode pressure based on the material’s thickness and properties.
- Electric Welding: Press the start button to initiate the high current through the electrodes. The contact point heats up quickly to the melting temperature, fusing the metal into a weld spot.
Cooling and Solidification Stage
- Stopping the Current: After the predetermined time, the machine automatically stops the current, allowing the weld spot to cool rapidly and solidify the materials.
- Releasing Pressure: Maintain the electrode pressure until the weld spot is completely solidified, then release the electrode pressure.
Inspection and Post-Processing
- Quality Inspection: Inspect the weld spot quality using visual checks, tensile tests, and other methods to ensure there are no defects like weak welds or burn-through.
- Post-Processing: If necessary, perform additional processing on the weld spots, such as grinding or coating.
Advantages of Spot Welding in Battery Production
- Speed and efficiency: for large-scale production
- Minimal heat affected zone: Reduces the risk of damage to sensitive battery components
- Strong and reliable connections: Crucial for battery pack integrity, spot welds are resistant to vibration, ensuring long-term reliability.
- No additional materials required: Spot welding doesn’t require additional materials like welding rods or gases, reducing costs.
Limitations of Spot Welding Lithium Ion Batteries
- Limited to conductive materials: Spot welding primarily works on electrically conductive materials. Non-conductive materials cannot be joined using this method.
- Material thickness: Spot welding is limited to joining thin sheets of metal. Thicker materials may require more powerful equipment or alternative welding techniques.
- High initial investment: Spot welding equipment can be expensive, especially for high-volume production.
- Operator expertise: Spot welding demands a high level of skill and precision from operators. Improper technique can lead to inconsistent weld quality, affecting battery performance and safety.
- Limited reach: Spot welding might be challenging for components located in tight or inaccessible areas of the battery pack.

Principles of Soldering in Lithium Battery Production
Soldering is a process used to join two or more metal components by melting a filler material (solder) into the joint. Unlike welding, the base metals do not melt during soldering. Instead, soldering relies on the filler material melting and forming a bond with the surface of the metals. The solder is applied to the heated joint area, where it melts and flows between the metal surfaces, solidifying to form a connection upon cooling.
Soldering Process
Preparation
- Cleaning the Surfaces: The surfaces of the components to be joined must be cleaned thoroughly to remove dirt, grease, oxides, and other contaminants. This ensures a strong bond and good electrical conductivity.
- Applying Flux: Apply a small amount of flux to the surfaces that will be soldered. This helps the solder flow more easily and adhere better to the metals.
Heating
- Heating the Soldering Iron: Allow the soldering iron or gun to heat up to the appropriate temperature for the solder being used. The temperature should be high enough to melt the solder but not so high as to damage the components.
- Applying Heat to the Joint: Place the tip of the soldering iron on the joint where the solder is to be applied. This heats the workpieces, ensuring the solder flows properly into the joint.
Applying Solder
- Feeding the Solder: Once the joint is hot enough, apply the solder to the joint. The solder should melt and flow into the joint, filling the gap between the components.
- Forming the Joint: Allow the solder to flow evenly around the joint, creating a smooth and uniform connection. Remove the soldering iron and allow the joint to cool and solidify.
Cooling and Inspection
- Cooling the Joint: Allow the soldered joint to cool naturally. Do not move the components during this time to prevent the formation of weak or cracked joints.
- Inspecting the Joint: After the joint has cooled, inspect it visually to ensure it is smooth, shiny, and free of defects such as cold joints, excess solder, or poor adhesion.
Advantages and Limitations of Soldering in Battery Production
Advantages:
- Ease of use: Lower skill requirement compared to spot welding.
- Lower heat impact: Soldering typically generates less overall heat during the process. This reduced heat can lower the risk of thermal stress and damage to sensitive battery components.
- Flexibility and Accessibility: Soldering allows for connections in tight or awkwardly positioned spaces where spot welding equipment might not fit. It’s adaptable to various battery designs and configurations, especially useful for custom or small-scale production.
- Reworkability: Easily reworked or repaired soldered connections if issues are found during quality control.
Limitations:
- Thermal Stress: While generally lower than spot welding, soldering can still subject battery components to thermal stress. If not performed correctly or suffers from excessive heat, this is problematic.
- Component Damage Risk: Improper soldering technique or excessive heat application can damage sensitive battery components. This damage can lead to reduced performance or even safety risks in the battery pack.
- Skill Requirement for Consistency: While soldering may be easier to learn initially, achieving consistently high-quality solder joints requires significant practice and skill development. Inconsistent quality can lead to reliability issues in the battery assembly.
- Flux Residue: Using flux in soldering leaves residues that need to be cleaned to prevent potential long-term issues like corrosion.
Comparing: Spot Welding vs Soldering
Aspect | Soldering | Spot Welding |
Heat Application | Externally applied heat using a soldering iron, gun, or furnace to melt the solder. | Heat is generated internally by the resistance of the metals to the electric current. |
Temperature | Lower temperatures are sufficient to melt the solder but not the base metals. | Lower temperatures are sufficient to melt the solder but not the base metals. |
Joint Type | It can be automated but is also commonly performed manually, especially for smaller or more delicate work. | lower temperatures are sufficient to melt the solder but not the base metals. |
Strength of Joint | Provides a reliable electrical connection but generally has lower mechanical strength compared to welding. | Produces a strong, permanent joint with high mechanical strength, suitable for structural applications. |
Materials Used | Common solder materials include tin, lead, silver, and copper alloys. Flux is also used to clean and prepare the surfaces. | Typically used for joining similar metal sheets like steel or aluminum without additional filler materials. |
Equipment Required | Soldering iron or gun, solder, and flux. Equipment is relatively simple and inexpensive. | Creates a point or spot joint where the metal sheets or parts are fused at specific points. |
Automation Capability | Can be automated but is also commonly performed manually, especially for smaller or more delicate work. | Highly suitable for automation, making it ideal for mass production in industries like automotive and aerospace. |
Skill Level Required | Requires a moderate to high skill level, especially for manual soldering, to ensure proper heat application and joint quality. | Requires less manual skill due to the automated nature of the process, but setup and programming require technical knowledge. |
Application Areas | Widely used in electronics, electrical wiring, plumbing, and fine metalwork. | Commonly used in automotive, aerospace, and sheet metal industries for assembling body panels and structural components |
Typical Defects | Cold joints, bridging, poor wetting, and excess solder. These can affect electrical connectivity and mechanical stability. | Incomplete fusion, electrode misalignment, and excessive indentation. These can weaken the joint and cause structural issues. |
Environmental Impact | Some solder materials contain lead, which is toxic. Lead-free solder options are available but may require higher temperatures. | No toxic materials are used in the process itself, but the electrical energy consumption can be significant. |
Quality Inspection | Visual inspection, electrical testing, and X-ray inspection are common methods to ensure joint quality. | Visual inspection and tensile testing are used to check the strength and integrity of the welds. |
Common Issues and Solutions: Spot Welding VS Soldering
Spot Welding often faces issues like poor weld quality, electrode wear, and excessive heat, which can lead to weak connections or damage. Solutions include optimizing welding parameters (current, pressure, and temperature), regular maintenance of electrodes, and ensuring clean, properly aligned contacts between components and electrodes.
Soldering issues include cold solder joints, bridging (short circuits), and oxidation, which can weaken electrical connections. Addressing problems by controlling heat application, using appropriate solder and flux, maintaining the cleanliness of the components and equipment, and selecting the right soldering techniques to ensure proper adhesion and avoid solder splatter. Using Laser technology for welding and cutting electrode materials in LiFePO4 battery packs.
As a custom battery pack manufacturer, we are well aware of the numerous challenges that arise in this process. We continually optimize our methods, provide training to our employees, reduce defects, and enhance the reliability and safety of our lithium battery packs.
CM Batteries’ Perspective on Spot Welding VS Soldering
At CM Batteries, we recognize that both spot welding and soldering are critical techniques in the production of lithium battery packs, each with distinct advantages and applications.
When deciding between spot welding and soldering for lithium battery production, consider the following factors:
- Production volume
- Design complexity
- The skill level and training requirements
- Equipment costs and maintenance
- Component heat sensitivity
- Quality and reliability requirements
- Regulatory compliance and safety standards
- Future scalability and adaptability
CM Batteries employs both techniques strategically, leveraging the strengths of each to optimize the performance, reliability, and safety of our battery packs.
Conclusion
When it comes to lithium battery production, both spot welding vs soldering play crucial roles. Spot welding excels in large-scale manufacturing scenarios where speed, reliability, and minimal heat input are crucial. Its ability to create strong connections quickly makes