With the growing applications for lithium batteries, the demand for high voltage, high rate, and high current has been increasing. However, it brings big challenges to improve the battery technology when the batteries are connected to the end devices with large capacitance (known as capacitive loads). When we start the turn-on button, the instantaneous start current across the terminal capacitors may cause an instant short-circuit, or sparking at the terminals. This is also known as ” Lithium Battery Sparking”.
Next, we’ll explore the importance of the pre-discharge function of the battery management system and protect the circuit protection from the peak currents.
Understanding the Capacitive Load of “Lithium Battery Sparking”
Terminal equipment often possesses a large capacitance, ranging from thousands to tens of thousands of μF. Although the voltage of the terminal capacitance does not change abruptly when the lithium battery pack is loaded, the current at both ends of the terminal capacitance experiences sudden fluctuations. This behavior is intrinsic to the working principle of a capacitor, resulting in an equivalent short-circuit at the terminal capacitor ends.
The Role of Pre-Discharge Circuits in Solving the Problem of Battery Sparked When Connected
To prevent dangerous high currents that surpass the normal operating current of the terminal equipment, it is essential to incorporate pre-discharge circuits into the lithium battery management system (BMS). By charging the capacitor with a limited current until it is fully charged, the pre-discharge circuit curbs the effects of peak currents. This prevents transient high currents well in excess of the normal operating current of the terminal equipment and avoids battery sparks when connecting. Effectively protects the circuit devices from peak currents.
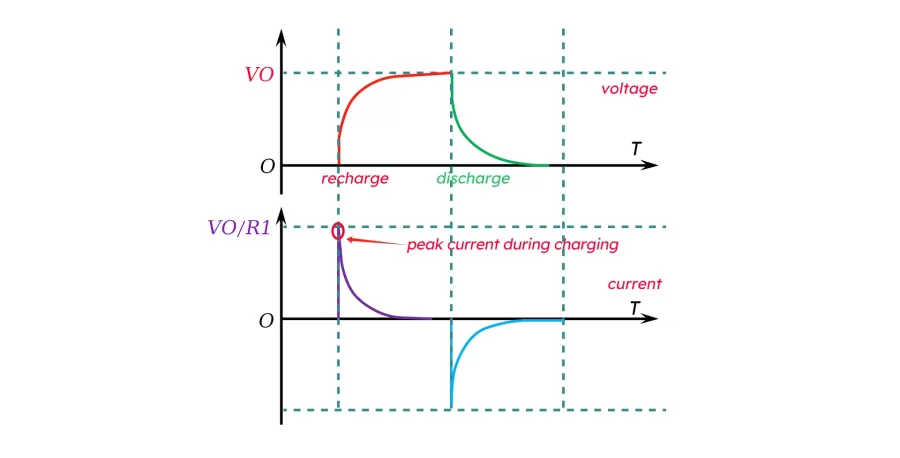
Pre-Discharge Function Operating Principle
The following outlines the operating principle of the pre-discharge function in the BMS solution:
- BMS receives the command to open the discharge circuit (Note 1).
- BMS initiates the pre-discharge circuit, which remains active for a specific duration, dependent on the capacitive load’s size.
- BMS closes the pre-discharge circuit and enables the normal discharge circuit.
To get the best performance from the pre-discharge function, two key factors must be considered. First, knowledge of the capacitive load’s size is necessary. Second, the pre-discharge function can only be activated once the battery has established a reliable connection with the capacitive load.
(Note 1: The command to open the discharge circuit can take the form of a communication instruction in the program or a hardware circuit pass-through. The precise method employed should align with the application scenario.)
Conclusion
The inclusion of pre-discharge circuits within lithium battery management systems plays a vital role in relieving the battery sparking when connecting problems caused by abrupt changes in current at both ends of the terminal capacitance. By performing this preventive function, the harmful effects of peak currents can be reduced, protecting the circuit device and ensuring its lifespan.
Our pre-discharge function for the BMS solutions they are used for the battery packs for electric surfboards, commercial and industrial cleaning machines, and big automatic robots.
Understanding the significance of pre-discharge functions and considering the specific parameters of the capacitive load are essential steps toward the safe and optimal utilization of lithium batteries in various applications.