As the world becomes more dependent on technology powered by lithium-ion batteries, the demand for more efficient and powerful battery packs is increasing. Series-parallel lithium-ion battery pack module design solutions are attracting the eyes of lithium battery pack engineers and the battery pack design industry for various applications.
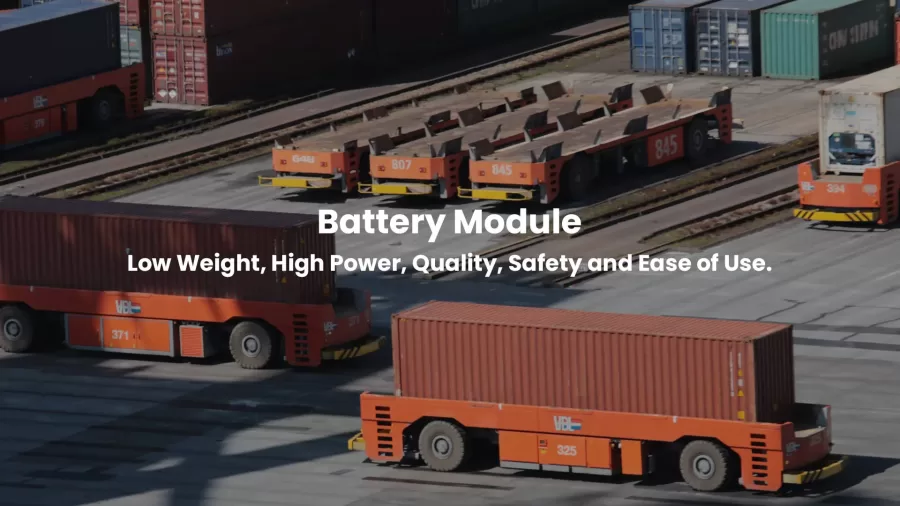
Why Do More Product Managers Prefer To Design Parallel, Series, And Series-Parallel Battery Packs?
In 2024, more people are opting for parallel, series, and series-parallel lithium-ion battery pack designs for two primary reasons:
1) Batteries with more than 100 watt hours (Wh) cannot be carried on board aircraft, thus making parallel, series, and series-parallel battery packs more optimal.
2) Parallel, series, and series-parallel battery pack designs offer a convenient replacement, portability, and flexible configuration for special applications such as for large outdoor equipment.
What Are Parallel, Series, And Series-Parallel Lithium-Ion Battery Packs?
1. Series Lithium-Ion Battery Packs
A series battery pack design, on the other hand, connects battery packs end-to-end to increase the voltage of the battery packs. The core advantage of the series rechargeable battery pack is that it has a higher voltage, while the disadvantage is that it has a lower capacity and discharge current when compared to parallel battery packs.
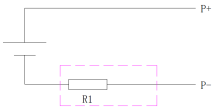
The dotted box in the figure above represents the BMS, where the resistor R1 represents the impedance of the MOS. When the MOS is on, the MOS is in a low-impedance state, assuming that R1 = 0.001Ω; when the MOS is not on, the MOS is in a high-impedance state, assuming that R1 = 1000MΩ.
Take 4 lithium batteries in series as an example, the schematic diagram after the series connection is simplified as follows.
Assuming that the voltage of each battery is 4V. If the BMS of all 4 batteries is in the conduction state.
That is, R1=R2=R3=R4=0.001Ω;
The voltage across each resistor is U1, U2, U3 and U4 respectively;
Then, U1=U2=U3=U4=4V.
If the BMS of the first of the 4 cells are all in a non-conducting state,
That is, R1=1000MΩ; R2=R3=R4=0.001Ω;
The voltage across each resistor is U1, U2, U3 and U4 respectively;
Then, U1≈16V; U2=U3=U4≈0V.
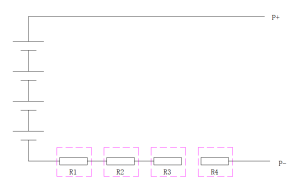
After the above analysis, the following conclusion can be obtained:
After multiple LiPo batteries are connected in series, if the BMS of one of the LiPo batteries triggers some kind of protection and the MOS switches to a high resistance state, the MOS terminals will withstand almost the entire voltage of the whole circuit. In this case, if the total voltage exceeds the limit of the MOS, then the MOS will burn up.
Therefore, only batteries that are designed to be connected in series are allowed to be connected in series, and the number of strings must not exceed the design value.
2. Parallel Lithium-Ion Battery Packs
A parallel battery pack design connects individual battery cells in parallel formation in order to increase the battery pack capacity. Parallel battery connection is commonly used in applications requiring high current output. The advantages of connecting batteries in parallel form include the ability to increase capacity and discharge currents. However, this design requires the development of significant technology for the battery management system (BMS).
Take 4 lithium batteries in parallel as an example, the simplified schematic diagram is as follows. The voltage of each battery is U1, U2, U3, U4; the internal resistance of each battery is R1, R2, R3, R4.
Assuming R1 = R2 = R3 = R4 = 0.03 Ω
Ideally U1=U2=U3=U4, the circuit works normally;
If U1>U2=U3=U4, then battery 1 will charge batteries 2, 3 and 4.
The charging current can be simplified as:
Charging current for batteries 2, 3, 4.
I2 = I3 = I4 = (U1 – U2) / (0.03 + 0.03/3) / 3
Assuming U1=12V, U2=U3=U4=9V, substituting the above formula gives:
I2=I3=I4=25A
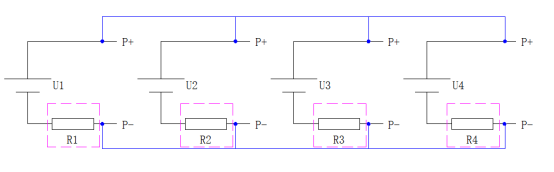
According to the above calculation, it can be concluded:
1. If the pressure difference is small enough when lithium batteries are connected in parallel, it is possible;
2. If the lithium battery is connected in parallel with a relatively large pressure difference, a large instantaneous current will be generated, which may damage the battery.
3. Series-Parallel Lithium-Ion Battery Packs
A series-parallel battery pack design combines the features of both parallel and series battery packs. This type of battery pack allows for increased voltage and capacity as well as a higher discharge current output. The primary disadvantage of the parallel-series battery connection is an increased cost.
Modular Vs Central Battery Management Systems (BMS): Which Is Better For Your Battery Pack Design?
While designing a battery management system (BMS), engineers must ensure that the battery cells maintain a good balance of cycles and working temperature. The battery cells need to keep the same state of charge (SOC) throughout the discharge and charge cycles. At CM Batteries, our CTO utilizes calculations and simulations to design systems that ensure battery pack safety and prolong the battery’s life cycles and reliability.
CM Batteries offers the following BMS design options:
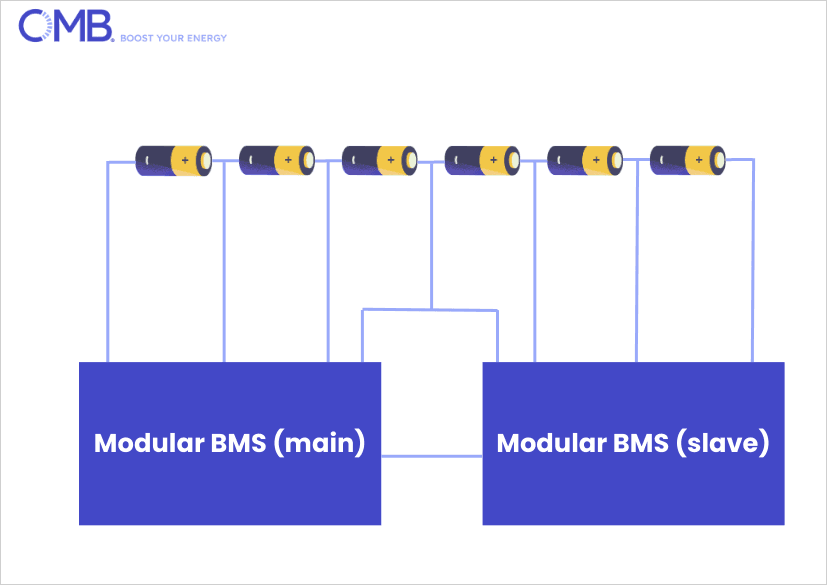
As shown in Figure 1, The modular BMS is divided into many identical sub-modules, and each pack features wires connecting different parts of the panel in order to monitor each particular area of the battery. One BMS module is assigned as the “master”, which is responsible for managing the scheduling of the whole pack and communicating with the outside world. The “slave” BMS communicates with the “master” BMS through the communication bus, but they both ultimately have the same function.
Advantages:
- Miniaturization of the centralized BMS: Features multiple cascades and most of the advantages of centralized BMS, including easy maintenance, less cost, etc.
- Smaller single module size: The sub-module to the single battery wire is relatively short and can be positioned closer to the battery to avoid hidden problems and errors caused by wires that are too long.
- Easy to expand: More sub-modules can be added to achieve expansion.
Disadvantages:
- Requires more wires than centralized BMS: A modular BMS not only needs to connect to the battery pack, but each module also needs to connect between the wires.
- Higher cost: Although the function of each module is the same, not all of the functions will be used, resulting in waste, especially considering the slave module has little use.
Because we feel that this design is not particularly efficient, CM Batteries offers an improved version of this BMS design, as demonstrated in Figure 2.
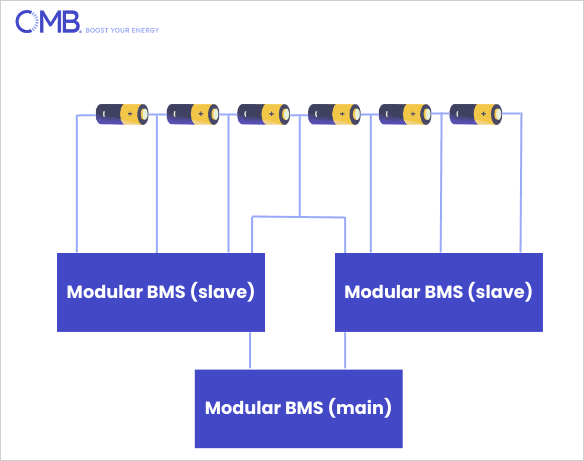
In this design, we separate the slave modules according to the different functions of the master and slave and remove the functions that are not used by the slave modules so that we can reduce costs significantly.
The main BMS is responsible for relatively more functions, such as calculation, prediction, decision-making, communication, etc. The slave module is responsible for measurement only. This design inherits most of the advantages of the modular structure, while also reducing the cost of expansion.
There is also a distributed BMS design solution available that features high connection reliability, no overly long cables, and tight integration of battery and measurement circuits to help reduce interference and errors. This model is safer. However, due to the high cost and highly complicated process, it’s not the design of choice for many customers.
Parallel, series, and series-parallel battery pack design options are becoming increasingly popular in battery pack solutions, especially for outdoor equipment applications. More people are expected to choose parallel, series, and series-parallel battery pack solutions throughout 2024 due to the limitations on the maximum current capacity of batteries on board flights and the convenience and flexibility these designs offer. Each model has its advantages and disadvantages, and careful battery management system (BMS) design is critical to ensure the safe operation, reliability, and extended life of each battery. Modular BMS design solutions can meet different requirements and reduce costs, and the engineers at CM Batteries are here to help you do just that.