In today’s rapidly evolving technological landscape, lithium batteries have emerged as the leading energy storage solution, particularly in electric applications. They power everything from electric vehicles (EVs) to grid-scale energy storage systems and are also critical in consumer electronics. Despite their prevalence, many manufacturers face challenges in managing the higher costs associated with lithium batteries compared to other battery chemistries. For Business-to-Business (B2B) companies operating in industries reliant on lithium batteries, understanding the factors behind Li-ion battery costs is essential for making informed decisions.
Why are Lithium Batteries so Expensive?
The lion battery cost has decreased in recent years. The average cost of an electric car battery is about $128/kWh in 2023, a significant decrease from $1,355/kWh in 2008. Lithium batteries are still the most expensive chemical materials, although their cost is decreasing. Here are the key factors affecting lithium battery pack costs:
Battery Cells (80% of Total Cost)
The individual battery cells constitute the largest portion of production expenses. Each cell consists of:
- Cathode
- Anode
- Electrolyte
- Separator
- Outer casing
The cathode materials and production processes are typically the most expensive components, and the less expensive components are the anode and separator. With the increasing demand for high-performance electronics, electric vehicles have led to scarcity and price fluctuations for key materials like lithium, cobalt, nickel, and manganese.
Challenges for Global Supply Chain
- Anticipated diminishing of global resources by 2050
- Environmental issues affecting lithium supplies (e.g., heatwaves in China)
- Ethical concerns surrounding cobalt mining in the Democratic Republic of Congo
- Political unrest in certain regions is restricting access to materials
These factors contribute to potential supply chain disruptions and drive costs at a high level for manufacturers.
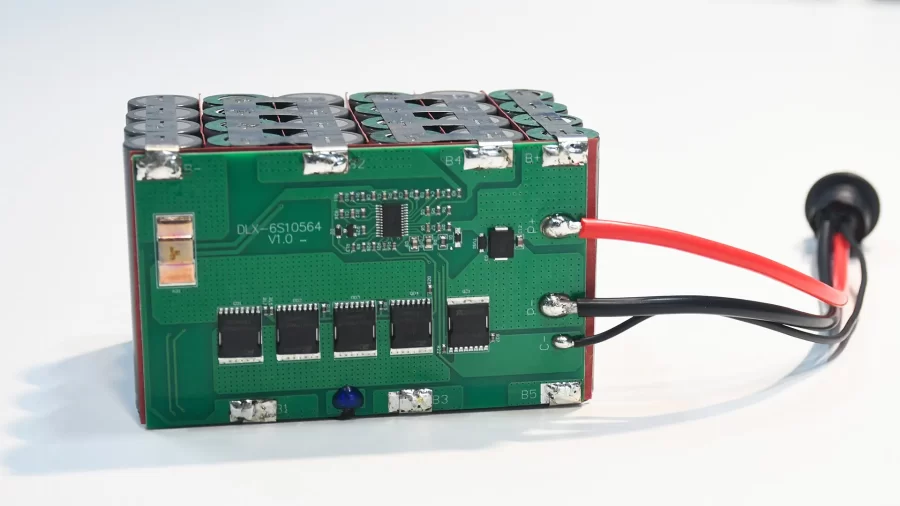
Battery Management System (BMS)
Compared to other chemistries, the li ion battery industry standards rule that all lithium-based chemistries should be integrated with a battery management system (BMS). The BMS is crucial for monitoring and protecting the battery, significantly impacting manufacturing costs. Protected Features can include:
- Basic monitoring (State of Charge, State of Health, temperature)
- Advanced features (cell balancing, real-time clocks, data logging)
BMS cost will vary depending on how many functionalities the customer requires. The basic BMS system will monitor SoC, SoH, and temperatures, whereas others may include cell balancing, real-time clocks, data recorders, and other capabilities. The price of the BMS will rise when more features are needed. Understanding the application’s power requirements can help clients select the specific functions in the BMS. More sophisticated systems with advanced functionalities increase overall Li-ion battery costs.
Integrated Circuits (ICs)
ICs play a vital role in charging and protecting lithium batteries. Different types of ICs, such as linear chargers and switch-mode chargers, offer varying levels of functionality and protection, impacting the overall cost. ICs not only charge the battery but also protect against overvoltage and overcurrent. They can keep the battery from charging too fast, exceeding its declared capacity, or overheating while charging.
Battery Charger
The lithium-ion battery cost chargers vary depending on whether customers wish to include a charger with the battery pack for immediate usage. Customers can choose whether to include a charger in the package or let end users choose by themselves.
Customized vs. off-the-shelf: Choosing between a customized charger and an off-the-shelf device has an impact on production costs. Customized chargers, intended to satisfy specific specifications, generally have greater production costs than ordinary, mass-produced off-the-shelf chargers.
Customers should carefully examine the trade-offs between including chargers with the battery pack and enabling users to choose their own. Furthermore, the choice between bespoke and off-the-shelf chargers should be based on the application’s specific requirements and financial limits to maximize overall cost-effectiveness.
Custom Battery Pack System
The battery pack system includes:
- Battery enclosure for protection or waterproof resistance
- Wiring harnesses
- Connectors
- BMS software
- Heating/cooling systems
The pack system ensures that the lithium cells provide power to the devices. While some components are standard, others are designed to satisfy special application requirements. Adding extra components or opting for higher-quality materials increases manufacturing costs but can boost performance and longevity. However, keep in mind that using cheaper materials, such as connectors, decreases performance and battery life. You must make a good balance between the lion battery price of designing and manufacturing the battery pack system to ensure performance and quality.
Testing, Certification, and Shipping
Lithium battery pack manufacturers must be certified with the safety certifications before shipping the batteries. Lithium-ion battery cost for testing and certification can vary significantly, typically ranging from $500 to $20,000, depending on the complexity and scope of certifications sought.
Testing Requirements: Both destructive and non-destructive testing may be performed throughout the certification process, with the battery pack for testing.
Manufacturer Changed or Battery Pack Redesign: If you change the battery pack manufacturer or battery pack redesign, the certificates will be redone, and the testing and battery certification.
Customers should calculate the bugs in the testing, certification, and shipping requirements. Allocating resources for thorough testing, certification processes, and potential redesigns can help mitigate unexpected costs and ensure compliance with industry regulations.
Lithium-ion Battery Costs Reduction Trends and Innovations
Manufacturers are actively working to reduce Li-ion battery costs without compromising performance:
1. Alternative Materials: Research into silicon-based anodes and alternative cathode materials (e.g., manganese or nickel) to reduce dependency on scarce resources.
2. Advanced Manufacturing Processes: Implementing more efficient production techniques to reduce waste and improve yield.
3. Improved Battery Designs: Developing new cell and pack designs that optimize performance while reducing material usage.
4. Recycling and Circular Economy: Investing in battery recycling technologies to recover valuable materials and reduce raw material costs.
5. Economies of Scale: As production volumes increase, per-unit costs are expected to decrease.
When you are searching for custom battery packs and chargers for the application’s power requirements, offer the specific needs of the battery pack manufacturer during the design phase. Furthermore, inviting your trustworthy battery pack manufacturer at the early design stages can help prevent manufacturing difficulties, which leads to optimizing your lithium-ion battery cost. If you have more questions, please feel free to ask!