How far away are we from solid-state batteries realistically? As the key technology for electrifying new energy vehicles, this battery is gradually moving from the lab to mass production, with large-scale commercial applications expected between 2027 and 2030. Currently, companies worldwide such as CATL, BYD, and Toyota are accelerating the development and mass production plans for solid-state batteries, making the competition fierce. It offers significantly better energy density, wider temperature range, and safety compared to traditional liquid lithium-ion batteries, but their high cost remains the primary hot topic for commercialization.
Solid-State Batteries in the Custom Battery Pack Market
Compared to traditional liquid batteries, solid-state batteries not only provide higher energy storage but also effectively reduce safety risks like fires, giving them broad application potential in new energy vehicles, energy storage, and more. Beyond the new energy vehicle market, it has huge potential in the custom battery market. From a technical perspective, custom battery packs are widely used in energy storage systems, industrial equipment, drones, medical devices, and other fields that demand higher performance, safety, and energy density. Solid-state batteries can handle greater energy loads without short circuits or explosions, significantly enhancing battery lifespan and stability.
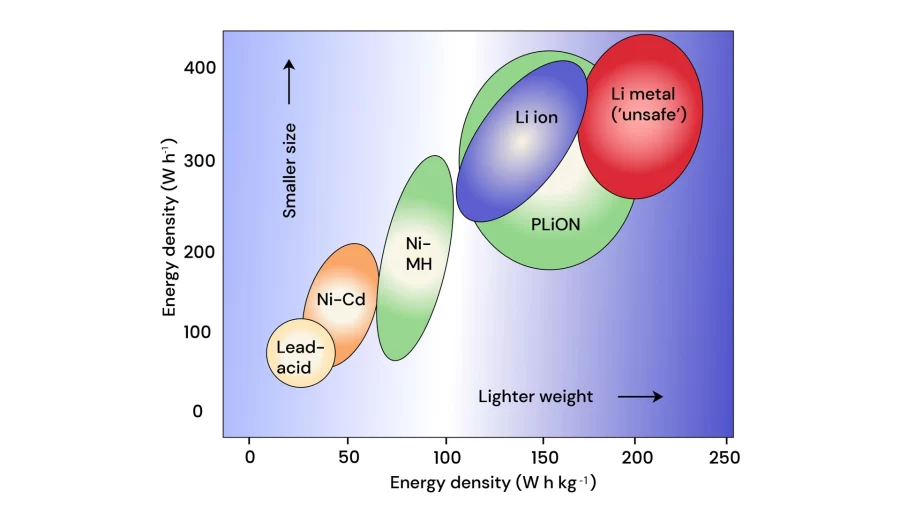
Technological R&D Capabilities
The performance of solid-state batteries largely depends on materials. Companies need the ability to develop high-performance solid electrolytes and electrode materials. For example, breakthroughs in sulfide electrolytes with high ionic conductivity and chemical stability, or finding electrode materials that pair well with solid electrolytes to boost energy density, like CATL’s advancements in sulfide and polymer electrolytes.
In battery design and integration, companies must design reasonable battery structures to address issues like solid-solid interface contact, heat dissipation, and volumetric energy density. Additionally, mass production of solid-state batteries faces challenges like lithium dendrite growth and interface compatibility between solid electrolytes and electrode materials. Companies must solve these problems by improving material formulations and optimizing processes.
Customization for Customer Needs
Custom battery pack customers often have specific performance requirements. Solid-state battery companies need to tailor designs and production to meet these demands, ensuring battery packs suit various application scenarios. Solid-state batteries’ higher energy density can provide longer runtimes for devices like drones and robots, which require high energy density to extend operational hours.
For energy storage systems, higher energy density means storing more electricity in the same volume or weight, improving overall efficiency. Solid-state batteries use solid electrolytes, eliminating the leakage and flammability risks of liquid electrolytes, and making them safer. This is crucial for fields like medical and industrial equipment, where safety is paramount.
In extreme environments (high/low temperatures, high humidity, etc.), solid-state batteries are more stable than traditional lithium-ion batteries, making them suitable for outdoor and military equipment.
Manufacturing Capabilities for Customization
The custom battery market often requires designs and production tailored to specific customer needs. The modular design and flexibility of solid-state batteries make them more adaptable to various shapes, sizes, and performance requirements. Suppliers need manufacturing capabilities that align with these demands.
In terms of process innovation and optimization, solid-state battery production differs from traditional lithium-ion batteries. Companies need to develop new processes, such as dry electrode manufacturing and solid electrolyte preparation and coating, while continuously optimizing to improve efficiency and product quality. For example, companies like Lyric Robot Automation Co., Ltd. have successfully developed full-process technologies for solid-state battery production, including dry electrode and electrolyte pressing equipment.
For quality control, companies must establish strict systems to ensure consistency and stability across raw material procurement, production, and product testing, meeting performance and safety standards.
Cost and Scalable Production
Current information indicates that solid-state batteries have higher production costs, particularly due to raw materials. Key materials like sulfide electrolytes require elements such as lithium, lanthanum, and zirconium. While lithium reserves are substantial, high-grade lithium resources are limited, and prices are sensitive to demand. Elements like lanthanum and zirconium are not found in high purity in nature, making their extraction complex and costly, driving up raw material expenses. Estimates suggest solid-state batteries are 4–10 times more expensive than equivalent lithium-ion batteries.
Additionally, solid-state battery production technology is still immature. For instance, the interface between solid electrolytes and electrode materials requires special handling, unlike the rapid assembly of traditional liquid batteries, reducing production efficiency and increasing per-unit costs. Specialized equipment, such as gloveboxes for handling moisture- and oxygen-sensitive materials, and costly physical/chemical vapor deposition systems for solid electrolyte films, further raise production costs.
These technical bottlenecks limit scalable production and slow market adoption. While some companies aim for solid-state battery mass production by 2027, transitioning to full commercialization will require extensive validation and optimization. Experts predict that even by 2030, while breakthroughs may enable large-scale use, it could take 20–30 years for solid-state batteries to fully replace liquid batteries and become mainstream. By then, costs may decrease to match or even undercut traditional lithium-ion batteries, opening more opportunities in the custom battery market.
In high-end custom markets (e.g., medical devices, aerospace), where cost sensitivity is lower and performance and safety are prioritized, solid-state batteries are likely to achieve commercialization first.
Supply Chain and Industry Collaboration
Mass production of solid-state batteries requires close collaboration across the supply chain, including raw material suppliers, battery manufacturers, and equipment makers. East Asia, led by China, South Korea, and Japan, continues to dominate lithium-ion battery innovation and production, while North America and Europe are investing heavily in local production to reduce reliance on East Asia. However, East Asia remains the most cost-effective and preferred choice. Custom battery market customers need stable supply chains, and solid-state battery production will drive industry-wide collaboration, enhancing supply chain stability and efficiency.
Conclusion
For solid-state battery technology to transition from the lab to large-scale commercial production, the focus of R&D must shift from optimizing the performance of individual batteries to integrating entire battery systems. This means not only improving single-cell performance but also ensuring they can be effectively combined into packs and systems. Battery management systems (BMS), mechanical structure optimization, and other system-level factors are now critical, as they directly impact safety, efficiency, and reliability. By prioritizing these system-level optimizations, manufacturers aim to deliver better solutions for large-scale applications like electric vehicles and grid storage.
Another key challenge is scaling production while reducing costs and maintaining scalability. The industry is working to streamline processes and develop scalable designs to ensure cost reductions don’t compromise performance.
Solid-state batteries hold immense potential not only in the new energy vehicle market but also in the custom battery market. However, their commercial success will depend on market validation. Companies must continuously improve R&D, manufacturing, quality control, and cost management to meet the diverse needs of custom battery users. For these users, solid-state batteries’ high energy density, safety, and flexibility will provide superior solutions, driving rapid growth in related industries.